Audi is pairing up with EOS who will implement modern 3D printing technology into automobile manufacturing. However, the German car manufacturer is also working with SLM and using their selective laser melting processes.
Over the course of 30 years, 3D printing has proven itself as a useful technology in the development of automobiles, as coverage on All3DP proves. Now Audi AG, the German automobile manufacturer, is expanding its 3D printing efforts to incorporate the technology even further.
Previously, Audi has used 3D printing for its motorsports division, creating equipment and building prototypes. But, to make sure they’re getting the most out of the technology, Audi has launched a development partnership with EOS, the additive manufacturing specialist.
EOS Additive Minds consulting division will work with Audi to implement 3D printing into its production. However, they’ll also be on hand to help with the development of a 3D printing center in Ingolstadt, Germany.
“The aim is to not only supply Audi with the right additive systems and processes but to also support them during applications development, when building up internal additive manufacturing (AM) knowledge and training their engineers to become in-house AM experts,” said Güngör Kara, Director of Global Application and Consulting at EOS.
However, EOS isn’t the only company working with Audi. SLM Solutions Group AG will also be collaborating with Audi who will be using their selective laser melting process. The technology will enable Audi to supply spare parts on demand.
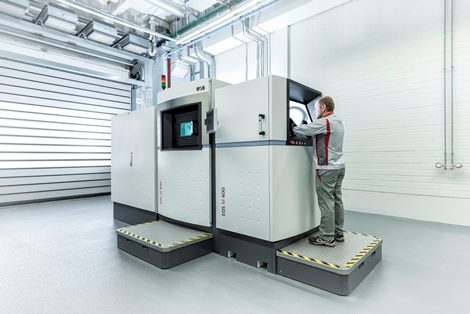
Producing Audi Parts in an On-Demand and Cost-Effective Manner
Audi explains that the reason for setting up the competence center is to learn more about 3D printing and gain experience with the processes and materials. Therefore, pairing with EOS was essential as they can provide guidance and support.
“With this technology, we are able to integrate internal structures and functions in tools that we have not been able to create so far with conventional manufacturing methods. Especially with components in small batches, we can now produce components using lightweight construction, quickly and economically based on this technology,” explains Jörg Spindler, head of Toolmaking at Audi.
An important vision for Audi to achieve is being able to manufacture on demand, supplying spare or complex parts which aren’t regularly required but are important nonetheless. By using 3D printing, they’re saving money and time, but also using a more sustainable technology.
“The new constructive freedoms provided by this technology are especially interesting… Components for prototypes and spare parts requested extremely rarely are better suited for SLM processes than conventional manufacturing procedures thanks to the benefits of free geometric design. The load capacity of the components is comparable with parts manufactured using traditional methods,” said Harald Eibisch, who works in the technology development department at Audi.
Source: Rapid Ready Tech
Website: LINK