GM is using Autodesk’s generative design technology and additive manufacturing to fabricate lighter automotive parts; this seat bracket is 40% lighter and 20% stronger than its predecessor.
General Motors is using generative design software by Autodesk to develop the next generation of lightweight vehicles. According to the automaker, the new technology will be a key factor in developing more efficient, alternative-fuel cars with zero emissions.
GM is the first automaker in North America to use the software. It uses cloud computing and AI-based algorithms to rapidly explore multiple permutations of a part design; it can generate hundreds of high-performance, often organic-looking geometric design options based on goals and parameters set by the user.
These parameters can include weight, strength, material choice, fabrication method, and more. Once generated, the user can then select and 3D print the best option from the available part designs.
“This disruptive technology provides tremendous advancements in how we can design and develop components for our future vehicles to make them lighter and more efficient,” says GM Vice President Ken Kelzer, Global Vehicle Components and Subsystems.
“When we pair the design technology with manufacturing advancements such as 3D printing, our approach to vehicle development is completely transformed and is fundamentally different to co-create with the computer in ways we simply couldn’t have imagined before.”
The new design technology provides significantly more vehicle mass reduction and parts consolidation, the likes of which cannot be achieved through traditional design optimization.
GM and Autodesk engineers have applied this new technology to produce a proof-of-concept part. They’ve demonstrated a new seat bracket that is 40 percent lighter and 20 percent stronger than the original part. It also consolidates eight different components into one 3D printed part.
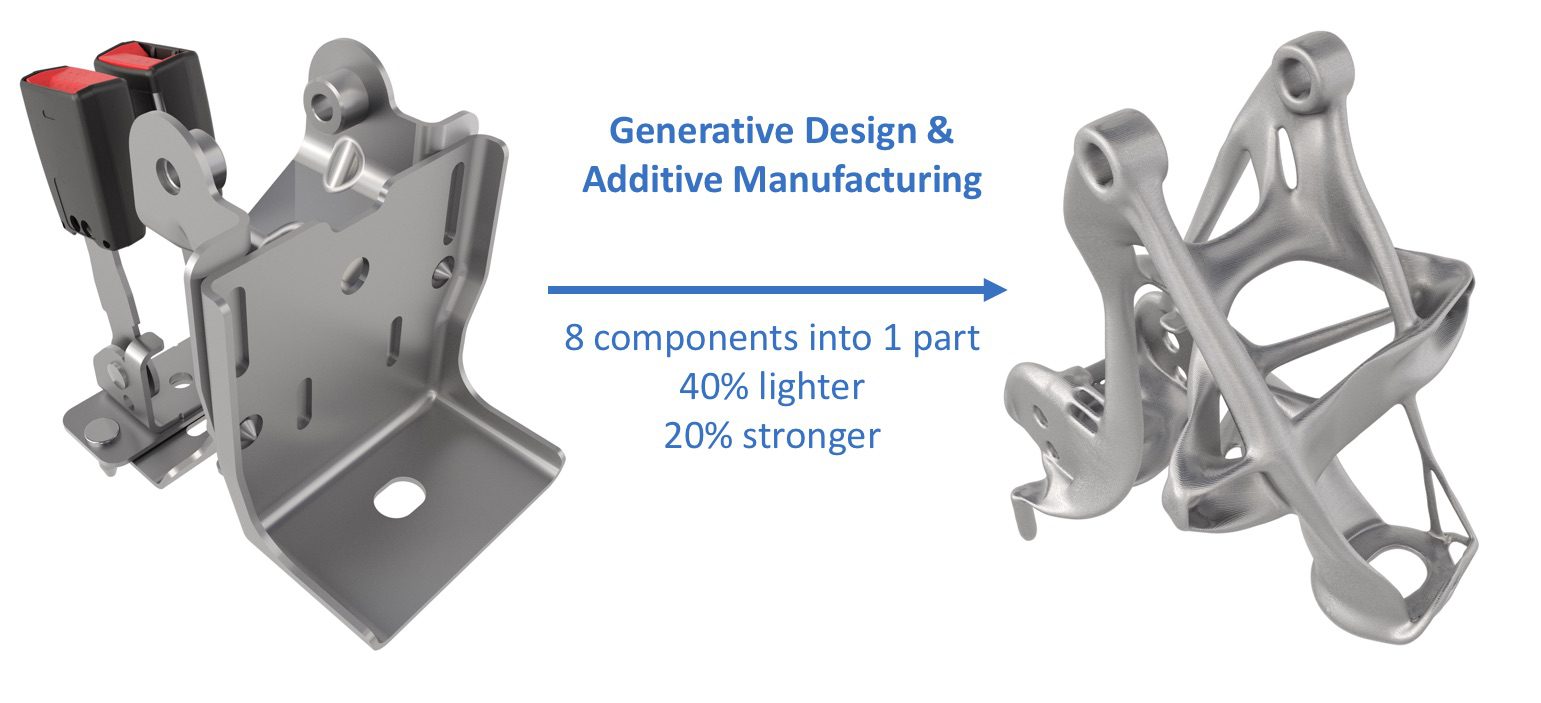
GM and Autodesk Entering Multi-year Alliance
GM has been a leading innovator in additive manufacturing for more than three decades. The automaker has one of the auto industry’s most comprehensive 3D printing capabilities in the world, with more than 50 rapid prototyping machines that have produced more than 250,000 prototype parts over the last decade.
Looking to the future in a multi-year alliance, GM and Autodesk will be collaborating on projects involving generative design, additive manufacturing, and materials science. Executives and engineers from both companies will participate in a series of onsite engagements to exchange ideas, learnings, and expertise.
“Generative design is the future of manufacturing, and GM is a pioneer in using it to lightweight their future vehicles,” says Scott Reese, Autodesk Senior Vice President for Manufacturing and Construction Products.
“Generative technologies fundamentally change how engineering work is done because the manufacturing process is built into design options from the start. GM engineers will be able to explore hundreds of ready-to-be-manufactured, high-performance design options faster than they were able to validate a single design the old way.”
Eliminating mass in parts where material is not required for performance — combined with parts consolidation — will bring many benefits for car owners. This includes the potential for more interior space, increased range, and enhanced vehicle performance. It also provides vehicle designers a canvas on which to explore designs and shapes like never before.
Source: Autodesk
Website: LINK