Blow Molding (also: Blow moulding) and the molding process of polymers is one of the pillars of industrial manufacturing. Without this technology, we wouldn’t have access to cheap glass or plastic bottles or mass-manufactured hollow containers.
Blow molding allows industry players to produce parts and containers fast and cheap in high quantities. But how does this process work and what has 3D printing to do with it? This article will give you all the answers in a nutshell.
What is Blow Molding?
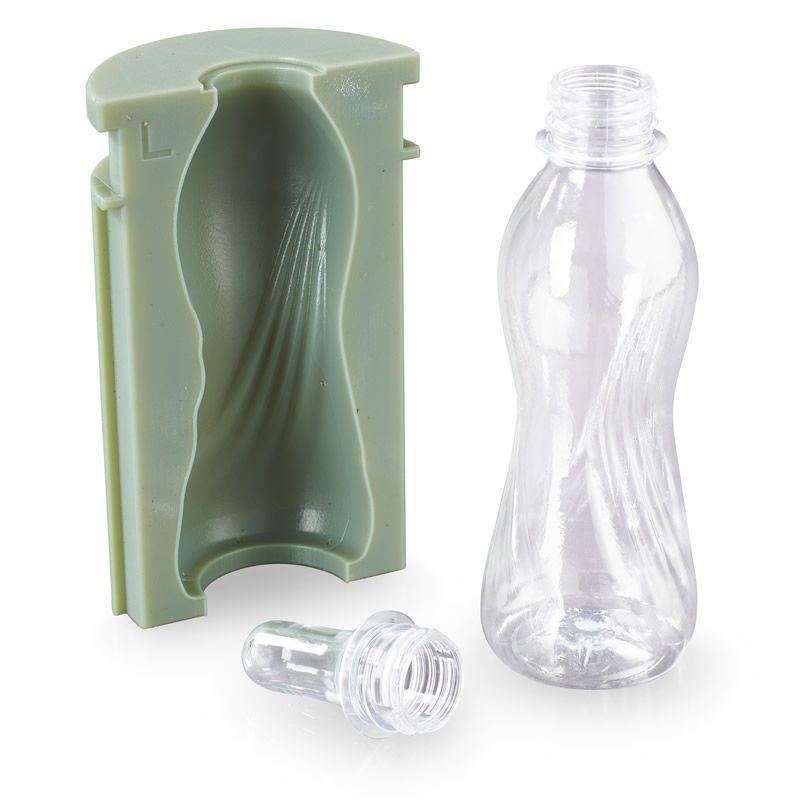
Blow molding started in the glass blowing industry where a liquid glass pulp is enclosed in a two-piece mold and then expanded by blowing into to the pulp. This causes the glass retains the contour of the mold and form a hollow area on the inside.
With the invention of polymeric thermoplastics, this technology started to rev up in the plastic bottle industry. Starting in 1977, the number of plastic containers rose from zero to 10 billion plastic bottles in 1999 due to the soft drink companies in the USA. The outcome isn’t exactly good for the environment, but if you use biodegradable materials or recycle thermoplastic bottles made from PET, things look a bit better.
Blow Molding versus Injection Molding
So, what’s the difference between parts made by injection molding and parts made by a blow molding machine? Injection molding creates solid parts, while blow molding creates hollow parts. If you are looking for something that needs only one rigid wall, injection molding is the right process. Think of bottle caps, cases, combs, and housings for computers and televisions. If you need a flexible, structural piece that even can hold fluid, you’re best off with blow molding. No wonder that billions of water bottles stand for the blow molding technology.
How Plastic Bottles are Made
Producing plastic bottles does not greatly differ from the glass blowing process. The technology used by the bottle forming process is called Injection Blow Molding (IBM). This requires a so-called preform which is much smaller than the actual bottle. The preform can be transported easily and if variants do not differ in weight it can be used uniformly. Like in the glass manufacturing process, the preform is heated up, put into the mold and inflated. Due to the preform, the material expands equally, resulting in a better flow control, surface quality and transparency. After the blow molding process, the bottle heads have to be threaded and the excess material cut off.
What are the Advantages of Blow Molding?
Blow molding scores especially at mass producing at a low price. Depending on the quality of the mold, it can produce more than over 1 million pieces before it has to be replaced. The production is also very fast compared to other molding processes, ejecting a finished product every few seconds. Thin walls and water-cooled molds also reduce cycle time. In addition, once the machine parameters are calibrated, the outputs quality is constant. This is achieved because factoring parameters are stable and controllable. The process of blow molding is also perfect for automation, reducing the need for workers working in a monotone environment.
What are the Limitations of Blow Molding?
Purchasing a molding machine may seem like the biggest investment of a company to start producing. However, before you start producing, you will need a mold. The biggest disadvantage of blow molding lies with the problem of all molding processes. For each type of product you want to produce, you need a new type of mold and this comes with a very steep price. The molds have to be machine milled and produced with a very high surface quality. The molds also have cannulas running through the walls to transport cooling fluids. In addition, the mold often has to be hardened to increase its lifespan. This high cost of molds often reduces a company’s incentive of producing prototypes, especially for low piece numbers.
How does 3D Printing Affect the Blow Molding Process?
This is where 3D printing comes in. With additive factoring, prototypes of molds can be produced faster and at a much lower cost. Unfortunately, 3D printed molds are way behind in durability than their machined counterparts. Still, it is not the goal to create a finished mold, but a prototype or a mold used only for small batches. In addition, it is less difficult and in extreme cases finally possible to create complex internal cooling pipes with 3D printing. The molds are made of metal with laser sintering or durable plastic with the Polyjet technology. The 3D printers of EOS or Stratasys are already helping to enhance the development of molds in all applications.
Which Businesses offer Blow Molding Technology?
If you are interested in acquiring a blow moulding machine or use a blow molding service, you have a choice of over 300 companies. Here are the most successful ones (according to Plastic News)
1. Amcor Rigid Plastics
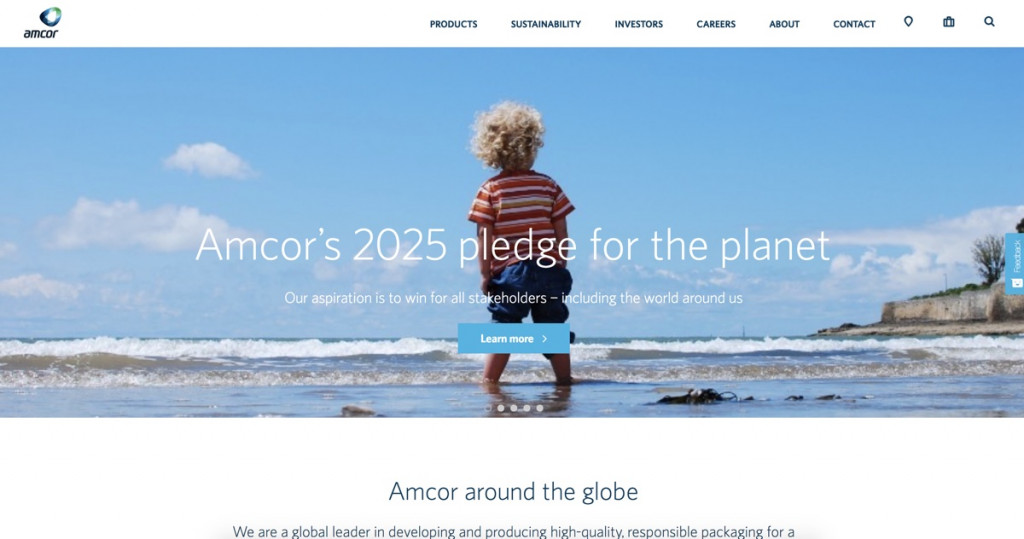
Company profile: Amcor Rigid Plastics is one of the leading manufacturing companies, developing and producing high-quality packaging for food, beverage, pharmaceutical, medical devices, personal care and other products. Blow molding is an integral part of the company. Amcor is currently offering its service in 200 production sites in 43 countries. 68 percent of the production are flexibles, 32 percent rigid products.
Blow molding sales: $2,26 million
More information: Here.
2. Graham Packaging
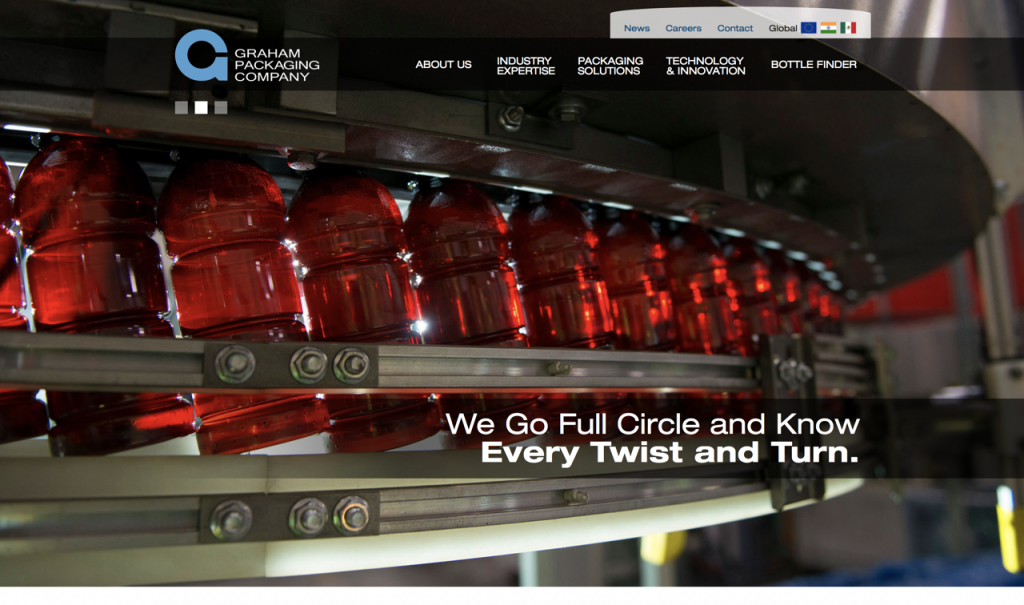
Company profile: What started in 1970 with a simple motor oil container, has become one of the most important companies in blow moulding business. The company offers bottles and containers for food, beverage, household, auto/chem, personal and healthcare businesses. Graham Packaging was early in PET technology and still innovating it today. Also, Graham is one of the world’s largest suppliers of bottle-grade recycled plastics.
Blow molding sales: $2,22 million
More information: Here.
3. Plastipak Packaging
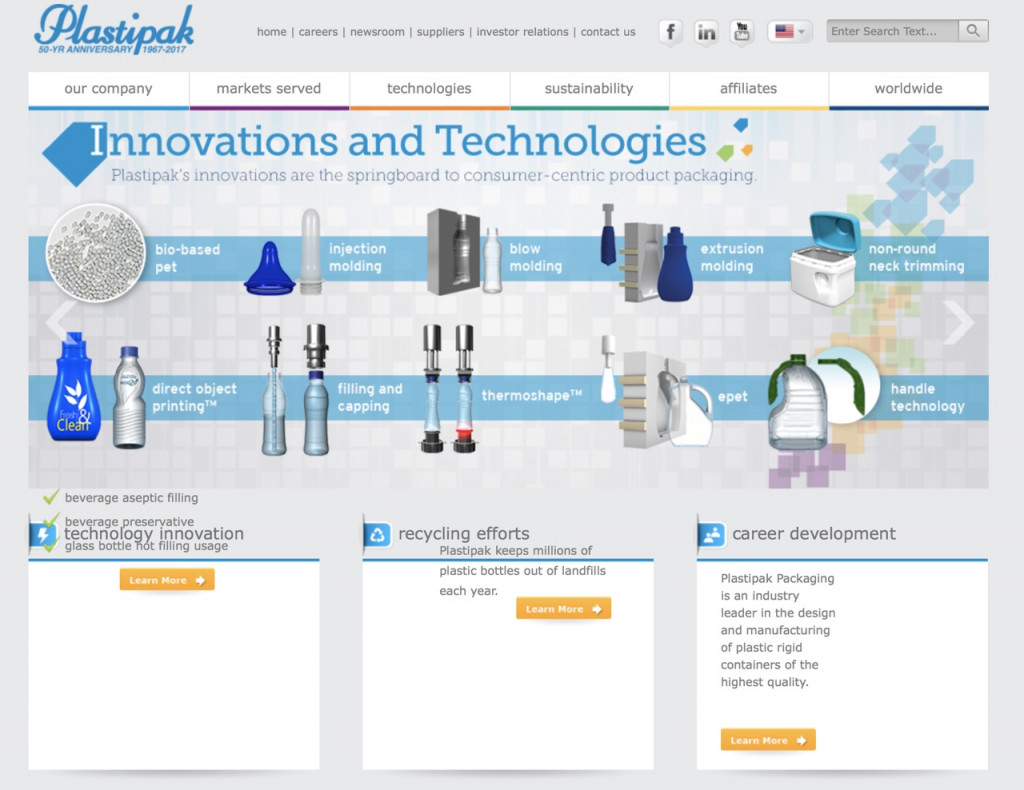
Company profile: With total annual sales of $2.7 billion, and more than 40.1 billion containers manufactured per year, Plastipak is one of the big players in blow molding. Founded in 1967, Plastipak started out providing plastic packaging to deliver water for the Young family’s water delivery company. Today, Plastipak now operates more than 60 production sites located in North America, South America, Europe, Africa, and Asia.
Blow molding sales: $1,64 million
More information: Here.
4. Plastic Omnium Auto Inergy Division

Company profile: The Auto Inergy Division is a subdivision of Plastic Omnium. They are manufacturing plastic fuel tank systems. The materials offer a combination of safety, cost, and weight performance (a 30% to 40% weight improvement compared with steel technologies), which are also usable in hybrid vehicles. Plastic Omnium offers solutions adapted for all kinds of engines.
Blow molding sales: $1,09 million
More information: Here.
5. Alpla

Company profile: Austria-based ALPLA Werke had a turnover of €3.4 billion in 2017 with 176 production facilities and 45 countries.. They are offering plastic packaging of all sorts, including packaging systems, bottles, closures, injection-molded parts, pre-forms, and tubes. Founded in 1955, Alpla claims to be “a family company steeped in tradition, always looking towards the future”.
Blow molding sales: $0,98 million
More information: Here.
Website: LINK